The heart of all organizational problem solving is to understand enough of the causes of the problem, and find an acceptable solution to it. Finding the “root cause or causes” of an organizational problem is the single most important determinant of success or failure of sustaining results. This is true of all types of problems: chronic problems that have been resistant to past solutions, day-to-day sporadic problems that have a tendency to recur, problems that involve identifying and eliminating waste—all require effective root cause analysis to reduce the risks and resistance associated with changing a process.
Organizational problem solving may not always be as complex as curing cancer, but at times you need to make risk-based decisions and get as close to the root causes as economically possible. We at Juran define a root cause as the cause(s) that addresses most of the problem that we as humans can control. A great example is the infamous Juran Institute Quality Minute about the Jefferson Memorial. The parks and recreation service of the US Government was dealing with high cost of maintenance of the park monuments. One in particular was the Jefferson Memorial. The building maintenance costs kept rising, and the service set out to discover why.
The Jefferson Memorial – Quality Minute
Root cause analysis is at the heart of all problem-solving methods, such as Six Sigma, Lean Problem Solving, and Plan, Do, Study/Check, Act. Root cause analysis is based on ‘’symptom-theory-cause.” Whether tackling daily problems or chronic problems, project teams must measure symptoms, theorize causes, and test those theories to prove root cause. The difference between methodologies are large problems need “sledgehammers and small problems need smaller hammers.” DMAIC is a sledgehammer and PDCA a hammer.
These problems differ from the larger, chronic problems that quality improvement programs such as Six Sigma focus on a comparison of the different methods to discover root causes and their uses is shown in the table below:
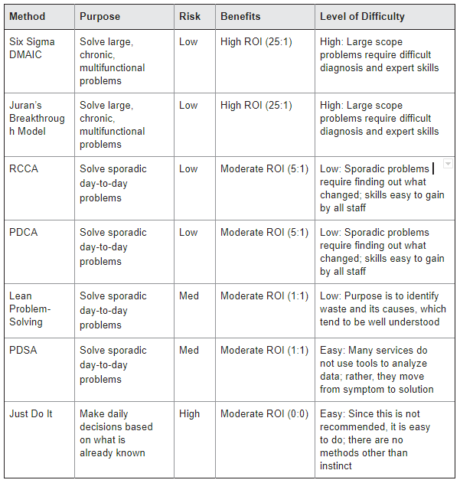
The lesson learned: use the right method, on the right problem, or you will waste time and money, and leaders will get frustrated that problems take too long to solve.
Looking to enhance and develop your skills? Want to learn how to take your organization to the next level? Want to earn a professional certification? Join us for our next open enrollment workshop! Check out the schedule here.
Check out Juran’s LSS Training Courses |
Lean Six Sigma Yellow Belt |
Lean Six Sigma Green Belt |
Lean Six Sigma Black Belt |
Upgrade to Black Belt |
Lean Six Sigma Master Black Belt |
Lean Expert Program |